Dank der rasanten Entwicklung der neuen Energiebranche hat das Laserschweißen in den letzten Jahren aufgrund seiner schnellen und stabilen Vorteile schnell die gesamte neue Energiebranche durchdrungen. Unter ihnen machen Laserschweißgeräte den höchsten Anwendungsanteil in der gesamten neuen Energiebranche aus.
Laserschweißenhat sich aufgrund seiner hohen Geschwindigkeit, großen Tiefe und geringen Verformung schnell zur ersten Wahl in allen Lebensbereichen entwickelt. Von Punktschweißungen über Stumpfschweißungen bis hin zu Auftrags- und Dichtschweißungen,Laserschweißenbietet beispiellose Präzision und Kontrolle. Es spielt eine wichtige Rolle in der industriellen Produktion und Fertigung, einschließlich der Militärindustrie, der medizinischen Versorgung, der Luft- und Raumfahrt, der 3C-Autoteileindustrie, der mechanischen Blechbearbeitung, der neuen Energiebranche und anderen Branchen.
Im Vergleich zu anderen Schweißtechnologien hat das Laserschweißen einzigartige Vor- und Nachteile.
Vorteil:
1. Schnelle Geschwindigkeit, große Tiefe und geringe Verformung.
2. Das Schweißen kann bei normaler Temperatur oder unter besonderen Bedingungen durchgeführt werden, und die Schweißausrüstung ist einfach. Beispielsweise driftet ein Laserstrahl nicht in einem elektromagnetischen Feld. Laser können in Vakuum-, Luft- oder bestimmten Gasumgebungen schweißen und können Materialien schweißen, die durch Glas hindurch oder für den Laserstrahl transparent sind.
3. Es kann feuerfeste Materialien wie Titan und Quarz schweißen und auch unterschiedliche Materialien mit guten Ergebnissen schweißen.
4. Nachdem der Laser fokussiert ist, ist die Leistungsdichte hoch. Das Seitenverhältnis kann 5:1 erreichen, beim Schweißen von Hochleistungsgeräten sogar bis zu 10:1.
5. Mikroschweißen kann durchgeführt werden. Nachdem der Laserstrahl fokussiert ist, kann ein kleiner Punkt erhalten und genau positioniert werden. Es kann beim Zusammenbau und Schweißen von Mikro- und Kleinwerkstücken eingesetzt werden, um eine automatisierte Massenproduktion zu erreichen.
6. Es kann schwer zugängliche Bereiche schweißen und berührungsloses Schweißen über große Entfernungen mit großer Flexibilität durchführen. Insbesondere in den letzten Jahren hat die YAG-Laserbearbeitungstechnologie die Glasfaserübertragungstechnologie übernommen, wodurch die Laserschweißtechnologie breiter gefördert und angewendet werden konnte.
7. Der Laserstrahl lässt sich zeitlich und räumlich leicht aufteilen, und mehrere Strahlen können gleichzeitig an mehreren Stellen bearbeitet werden, was die Voraussetzungen für präziseres Schweißen schafft.
Defekt:
1. Die Montagegenauigkeit des Werkstücks muss hoch sein und die Position des Balkens auf dem Werkstück darf nicht wesentlich abweichen. Dies liegt daran, dass die Laserpunktgröße nach der Fokussierung klein und die Schweißnaht schmal ist, was das Hinzufügen von Zusatzwerkstoffen erschwert. Wenn die Montagegenauigkeit des Werkstücks oder die Positionierungsgenauigkeit des Trägers nicht den Anforderungen entspricht, kann es zu Schweißfehlern kommen.
2. Die Kosten für Laser und zugehörige Systeme sind hoch und die einmalige Investition ist groß.
Häufige Fehler beim Laserschweißenin der Herstellung von Lithiumbatterien
1. Schweißporosität
Häufige Mängel inLaserschweißensind Poren. Das Schweißbad ist tief und schmal. Beim Laserschweißen dringt Stickstoff von außen in das Schmelzbad ein. Während des Abkühl- und Erstarrungsprozesses des Metalls nimmt die Löslichkeit von Stickstoff mit sinkender Temperatur ab. Wenn das geschmolzene Metall im Pool abkühlt und zu kristallisieren beginnt, sinkt die Löslichkeit stark und plötzlich. Zu diesem Zeitpunkt fällt eine große Menge Gas aus und bildet Blasen. Wenn die Schwebegeschwindigkeit der Blasen geringer ist als die Kristallisationsgeschwindigkeit des Metalls, entstehen Poren.
Bei Anwendungen in der Lithiumbatterieindustrie stellen wir oft fest, dass Poren besonders wahrscheinlich beim Schweißen der positiven Elektrode auftreten, beim Schweißen der negativen Elektrode jedoch selten. Dies liegt daran, dass die positive Elektrode aus Aluminium und die negative Elektrode aus Kupfer besteht. Während des Schweißens kondensiert das flüssige Aluminium an der Oberfläche, bevor das innere Gas vollständig überläuft, wodurch verhindert wird, dass das Gas überläuft und große und kleine Löcher bildet. Kleine Spaltöffnungen.
Zusätzlich zu den oben genannten Ursachen für Poren gehören zu den Poren auch Außenluft, Feuchtigkeit, Oberflächenöl usw. Darüber hinaus beeinflussen auch die Richtung und der Winkel des Einblasens von Stickstoff die Bildung von Poren.
Wie lässt sich das Auftreten von Schweißporen reduzieren?
Erstens, vorherSchweißen, müssen die Ölflecken und Verunreinigungen auf der Oberfläche der eingehenden Materialien rechtzeitig gereinigt werden; Bei der Produktion von Lithiumbatterien ist die Materialeingangskontrolle ein wesentlicher Prozess.
Zweitens sollte der Schutzgasfluss an Faktoren wie Schweißgeschwindigkeit, Leistung, Position usw. angepasst werden und weder zu groß noch zu klein sein. Der Schutzmanteldruck sollte abhängig von Faktoren wie Laserleistung und Fokusposition angepasst werden und weder zu hoch noch zu niedrig sein. Die Form der Schutzmanteldüse sollte entsprechend der Form, Richtung und anderen Faktoren der Schweißnaht angepasst werden, damit der Schutzmantel den Schweißbereich gleichmäßig abdecken kann.
Drittens kontrollieren Sie die Temperatur, Luftfeuchtigkeit und den Staub in der Luft in der Werkstatt. Die Umgebungstemperatur und -feuchtigkeit beeinflussen den Feuchtigkeitsgehalt auf der Oberfläche des Substrats und des Schutzgases, was wiederum die Entstehung und das Entweichen von Wasserdampf im Schmelzbad beeinflusst. Bei zu hoher Umgebungstemperatur und Luftfeuchtigkeit entsteht zu viel Feuchtigkeit auf der Oberfläche des Substrats und des Schutzgases, wodurch viel Wasserdampf entsteht und Poren entstehen. Wenn die Umgebungstemperatur und die Luftfeuchtigkeit zu niedrig sind, gibt es zu wenig Feuchtigkeit auf der Oberfläche des Substrats und im Schutzgas, was die Bildung von Wasserdampf verringert und dadurch die Poren verkleinert. Lassen Sie das Qualitätspersonal den Zielwert für Temperatur, Luftfeuchtigkeit und Staub an der Schweißstation ermitteln.
Viertens wird die Strahlschwenkmethode verwendet, um Poren beim Laser-Tiefschweißen zu reduzieren oder zu beseitigen. Aufgrund der zusätzlichen Schwingung während des Schweißens führt die Hin- und Herbewegung des Strahls zur Schweißnaht zu einem wiederholten Umschmelzen eines Teils der Schweißnaht, was die Verweilzeit des flüssigen Metalls im Schweißbad verlängert. Gleichzeitig erhöht sich durch die Ablenkung des Strahls auch der Wärmeeintrag pro Flächeneinheit. Das Tiefen-zu-Breiten-Verhältnis der Schweißnaht verringert sich, was die Blasenbildung begünstigt und Poren beseitigt. Andererseits führt die Schwingung des Strahls dazu, dass das kleine Loch entsprechend schwingt, was auch eine Rührkraft für das Schweißbad erzeugen, die Konvektion und Rührung des Schweißbades erhöhen und sich positiv auf die Porenbeseitigung auswirken kann.
Fünftens, die Pulsfrequenz, die Pulsfrequenz bezieht sich auf die Anzahl der vom Laserstrahl pro Zeiteinheit emittierten Pulse, die den Wärmeeintrag und die Wärmeakkumulation im Schmelzbad beeinflussen und dann das Temperaturfeld und das Strömungsfeld in der Schmelze beeinflussen Pool. Eine zu hohe Pulsfrequenz führt zu einem übermäßigen Wärmeeintrag in das Schmelzbad, wodurch die Temperatur des Schmelzbades zu hoch wird und Metalldampf oder andere bei hohen Temperaturen flüchtige Elemente entstehen, wodurch Poren entstehen. Eine zu niedrige Pulsfrequenz führt zu einer unzureichenden Wärmespeicherung im Schmelzbad, wodurch die Temperatur des Schmelzbades zu niedrig wird, die Auflösung und das Entweichen von Gas verringert werden und Poren entstehen. Im Allgemeinen sollte die Pulsfrequenz in einem angemessenen Bereich basierend auf der Substratdicke und der Laserleistung gewählt werden und weder zu hoch noch zu niedrig sein.
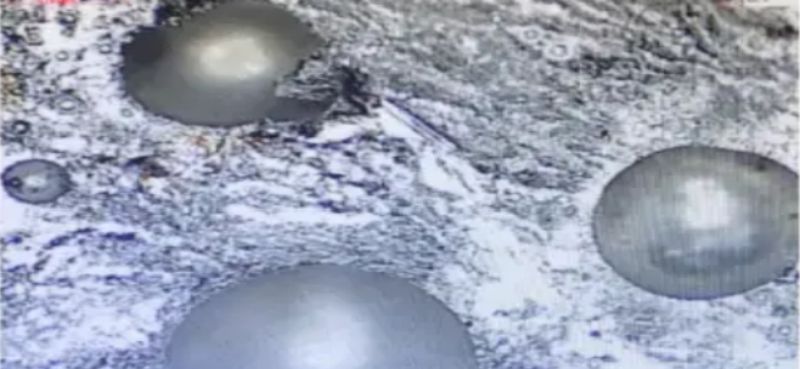
Löcher schweißen (Laserschweißen)
2. Schweißspritzer
Die beim Laserschweißen entstehenden Spritzer beeinträchtigen die Oberflächenqualität der Schweißnaht erheblich und verunreinigen und beschädigen die Linse. Die allgemeine Leistung ist wie folgt: Nach Abschluss des Laserschweißens erscheinen viele Metallpartikel auf der Oberfläche des Materials oder Werkstücks und haften an der Oberfläche des Materials oder Werkstücks. Die intuitivste Leistung besteht darin, dass beim Schweißen im Galvanometermodus nach einiger Zeit der Verwendung der Schutzlinse des Galvanometers dichte Grübchen auf der Oberfläche entstehen, die durch Schweißspritzer verursacht werden. Nach längerer Zeit blockiert das Licht leicht und es kommt zu Problemen mit dem Schweißlicht, was zu einer Reihe von Problemen wie gebrochenem Schweißen und virtuellem Schweißen führt.
Was sind die Ursachen für Spritzer?
Erstens ist die Leistungsdichte umso größer, je größer die Leistungsdichte ist, desto leichter ist es, Spritzer zu erzeugen, und die Spritzer stehen in direktem Zusammenhang mit der Leistungsdichte. Das ist ein jahrhundertealtes Problem. Zumindest bisher konnte die Branche das Spritzwasserproblem nicht lösen und kann nur von einer leichten Reduzierung sprechen. In der Lithiumbatterieindustrie sind Spritzwasser die Hauptursache für Batteriekurzschlüsse, die Ursache konnte jedoch nicht gelöst werden. Die Auswirkungen von Spritzern auf die Batterie können nur unter dem Gesichtspunkt des Schutzes verringert werden. Beispielsweise wird rund um das Schweißteil ein Kreis aus Staubabsaugöffnungen und Schutzabdeckungen angebracht, und in Kreisen werden Reihen von Luftmessern angebracht, um die Auswirkungen von Spritzern oder sogar Schäden an der Batterie zu verhindern. Man kann sagen, dass die Zerstörung der Umwelt, Produkte und Komponenten rund um die Schweißstation die Mittel erschöpft hat.
Was die Lösung des Spritzerproblems angeht, kann man nur sagen, dass eine Reduzierung der Schweißenergie zur Reduzierung der Spritzer beiträgt. Auch eine Reduzierung der Schweißgeschwindigkeit kann helfen, wenn der Einbrand nicht ausreicht. Bei einigen speziellen Prozessanforderungen hat es jedoch nur geringe Auswirkungen. Es ist der gleiche Prozess, unterschiedliche Maschinen und unterschiedliche Materialchargen haben völlig unterschiedliche Schweißeffekte. Daher gibt es in der neuen Energiebranche eine ungeschriebene Regel: ein Satz Schweißparameter für ein Gerät.
Zweitens: Wenn die Oberfläche des bearbeiteten Materials oder Werkstücks nicht gereinigt wird, können auch Ölflecken oder Schadstoffe schwere Spritzer verursachen. Zu diesem Zeitpunkt ist es am einfachsten, die Oberfläche des verarbeiteten Materials zu reinigen.
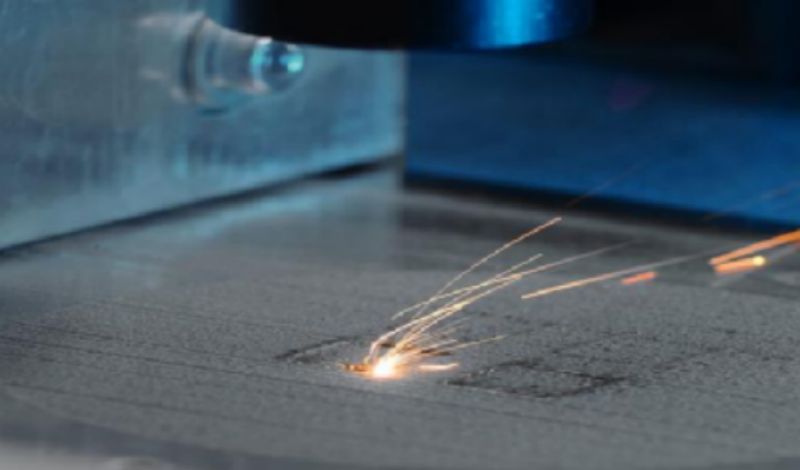
3. Hohes Reflexionsvermögen beim Laserschweißen
Im Allgemeinen bezieht sich eine hohe Reflexion auf die Tatsache, dass das Verarbeitungsmaterial einen geringen spezifischen Widerstand, eine relativ glatte Oberfläche und eine niedrige Absorptionsrate für Nahinfrarotlaser aufweist, was zu einer großen Laseremission führt, und darauf, dass die meisten Laser verwendet werden In vertikaler Richtung gelangt das zurückkommende Laserlicht aufgrund des Materials oder einer geringen Neigung wieder in den Ausgangskopf, wobei sogar ein Teil des zurückkommenden Lichts in die energieübertragende Faser eingekoppelt und entlang der Faser nach innen zurückgeleitet wird des Lasers, wodurch die Kernkomponenten im Inneren des Lasers weiterhin eine hohe Temperatur aufweisen.
Wenn das Reflexionsvermögen beim Laserschweißen zu hoch ist, können folgende Lösungen ergriffen werden:
3.1 Verwenden Sie eine Antireflexionsbeschichtung oder behandeln Sie die Oberfläche des Materials: Durch die Beschichtung der Oberfläche des Schweißmaterials mit einer Antireflexionsbeschichtung kann das Reflexionsvermögen des Lasers wirksam verringert werden. Bei dieser Beschichtung handelt es sich in der Regel um ein spezielles optisches Material mit geringem Reflexionsvermögen, das Laserenergie absorbiert, anstatt sie zurückzureflektieren. Bei manchen Verfahren wie Stromabnehmerschweißen, Soft-Connection etc. kann die Oberfläche auch geprägt werden.
3.2 Schweißwinkel anpassen: Durch Anpassen des Schweißwinkels kann der Laserstrahl in einem geeigneteren Winkel auf das Schweißmaterial treffen und das Auftreten von Reflexionen reduzieren. Normalerweise ist ein senkrechter Einfall des Laserstrahls auf die Oberfläche des zu verschweißenden Materials eine gute Möglichkeit, Reflexionen zu reduzieren.
3.3 Zugabe von Hilfsabsorptionsmittel: Während des Schweißvorgangs wird der Schweißnaht eine bestimmte Menge Hilfsabsorptionsmittel, beispielsweise Pulver oder Flüssigkeit, zugesetzt. Diese Absorber absorbieren Laserenergie und verringern das Reflexionsvermögen. Basierend auf den spezifischen Schweißmaterialien und Anwendungsszenarien muss das geeignete Absorptionsmittel ausgewählt werden. In der Lithiumbatterieindustrie ist dies unwahrscheinlich.
3.4 Lichtwellenleiter zur Laserübertragung verwenden: Wenn möglich, kann zur Reduzierung des Reflexionsvermögens Lichtwellenleiter zur Laserübertragung zur Schweißposition verwendet werden. Optische Fasern können den Laserstrahl zum Schweißbereich leiten, um eine direkte Einwirkung auf die Oberfläche des Schweißmaterials zu vermeiden und das Auftreten von Reflexionen zu reduzieren.
3.5 Anpassen der Laserparameter: Durch Anpassen von Parametern wie Laserleistung, Brennweite und Fokusdurchmesser kann die Verteilung der Laserenergie gesteuert und Reflexionen reduziert werden. Bei einigen reflektierenden Materialien kann die Reduzierung der Laserleistung eine effektive Möglichkeit sein, Reflexionen zu reduzieren.
3.6 Strahlteiler verwenden: Ein Strahlteiler kann einen Teil der Laserenergie in die Absorptionseinrichtung leiten und so das Auftreten von Reflexionen reduzieren. Strahlteilungsgeräte bestehen normalerweise aus optischen Komponenten und Absorbern. Durch die Auswahl geeigneter Komponenten und die Anpassung der Anordnung des Geräts kann ein geringeres Reflexionsvermögen erreicht werden.
4. Schweißunterschnitt
Bei welchen Prozessen im Herstellungsprozess von Lithiumbatterien ist die Wahrscheinlichkeit größer, dass es zu Unterbietungen kommt? Warum kommt es zur Unterbietung? Lassen Sie es uns analysieren.
Unterschnitt, im Allgemeinen sind die Schweißrohstoffe nicht gut miteinander verbunden, der Spalt ist zu groß oder es entsteht eine Nut, die Tiefe und Breite sind grundsätzlich größer als 0,5 mm, die Gesamtlänge beträgt mehr als 10 % der Schweißnahtlänge oder größer als der Produktprozessstandard ist die gewünschte Länge.
Im gesamten Herstellungsprozess von Lithiumbatterien ist es wahrscheinlicher, dass eine Unterschneidung auftritt, und sie verteilt sich im Allgemeinen auf das abdichtende Vorschweißen und Schweißen der zylindrischen Abdeckplatte und das abdichtende Vorschweißen und Schweißen der quadratischen Aluminiumgehäuse-Abdeckplatte. Der Hauptgrund besteht darin, dass die Dichtungsabdeckplatte zum Schweißen mit der Schale zusammenarbeiten muss. Der Passvorgang zwischen der Dichtungsabdeckplatte und der Schale ist anfällig für übermäßige Schweißspalte, Rillen, Kollaps usw. und daher besonders anfällig für Hinterschneidungen .
Was verursacht also eine Unterbietung?
Wenn die Schweißgeschwindigkeit zu hoch ist, hat das flüssige Metall hinter dem kleinen Loch, das zur Mitte der Schweißnaht zeigt, keine Zeit, sich neu zu verteilen, was zu einer Verfestigung und Unterschneidung auf beiden Seiten der Schweißnaht führt. Angesichts der oben genannten Situation müssen wir die Schweißparameter optimieren. Vereinfacht ausgedrückt handelt es sich dabei um wiederholte Experimente, um verschiedene Parameter zu überprüfen und so lange DOE durchzuführen, bis die geeigneten Parameter gefunden sind.
2. Zu große Schweißspalten, Rillen, Einbrüche usw. der Schweißmaterialien verringern die Menge an geschmolzenem Metall, die die Lücken füllt, wodurch die Wahrscheinlichkeit von Hinterschneidungen steigt. Das ist eine Frage der Ausrüstung und der Rohstoffe. Ob die Schweißrohstoffe den eingehenden Materialanforderungen unseres Prozesses entsprechen, ob die Genauigkeit der Ausrüstung den Anforderungen entspricht usw. Die übliche Praxis besteht darin, die Lieferanten und die für die Ausrüstung verantwortlichen Personen ständig zu foltern und zu schlagen.
3. Wenn die Energie am Ende des Laserschweißens zu schnell abfällt, kann das kleine Loch kollabieren, was zu einer lokalen Unterätzung führt. Durch die richtige Abstimmung von Leistung und Geschwindigkeit kann die Entstehung von Hinterschneidungen wirksam verhindert werden. Wie das alte Sprichwort sagt: Wiederholen Sie Experimente, überprüfen Sie verschiedene Parameter und fahren Sie mit der DOE fort, bis Sie die richtigen Parameter gefunden haben.
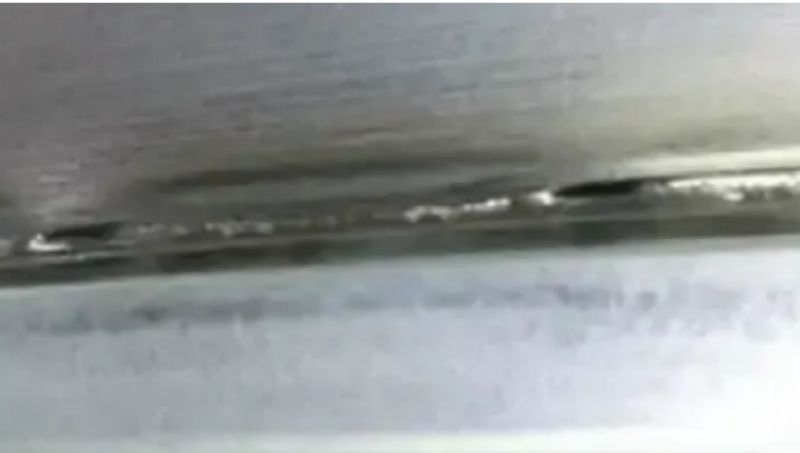
5. Zusammenbruch des Schweißzentrums
Wenn die Schweißgeschwindigkeit langsam ist, wird das Schmelzbad größer und breiter, wodurch sich die Menge an geschmolzenem Metall erhöht. Dies kann die Aufrechterhaltung der Oberflächenspannung erschweren. Wenn die Metallschmelze zu schwer wird, kann die Mitte der Schweißnaht einsinken und Vertiefungen und Vertiefungen bilden. In diesem Fall muss die Energiedichte entsprechend reduziert werden, um einen Zusammenbruch des Schmelzbades zu verhindern.
In einer anderen Situation bildet der Schweißspalt lediglich einen Kollaps, ohne dass es zu einer Perforation kommt. Dies ist zweifellos ein Problem der Presspassung der Ausrüstung.
Ein richtiges Verständnis der Fehler, die beim Laserschweißen auftreten können, und der Ursachen verschiedener Fehler ermöglicht einen gezielteren Ansatz zur Lösung abnormaler Schweißprobleme.
6. Schweißrisse
Bei den Rissen, die beim kontinuierlichen Laserschweißen auftreten, handelt es sich hauptsächlich um thermische Risse, wie zum Beispiel Kristallrisse und Verflüssigungsrisse. Die Hauptursache für diese Risse sind die großen Schrumpfkräfte, die die Schweißnaht vor ihrer vollständigen Erstarrung erzeugt.
Darüber hinaus gibt es folgende Gründe für Risse beim Laserschweißen:
1. Unangemessene Schweißnahtkonstruktion: Eine unsachgemäße Gestaltung der Geometrie und Größe der Schweißnaht kann zu einer Konzentration der Schweißspannung und damit zu Rissen führen. Die Lösung besteht darin, das Schweißdesign zu optimieren, um Schweißspannungskonzentrationen zu vermeiden. Sie können geeignete versetzte Schweißnähte verwenden, die Schweißnahtform ändern usw.
2. Nicht übereinstimmende Schweißparameter: Eine falsche Auswahl der Schweißparameter, wie z. B. zu hohe Schweißgeschwindigkeit, zu hohe Leistung usw., kann zu ungleichmäßigen Temperaturänderungen im Schweißbereich führen, was zu großen Schweißspannungen und Rissen führt. Die Lösung besteht darin, die Schweißparameter an das jeweilige Material und die Schweißbedingungen anzupassen.
3. Schlechte Vorbereitung der Schweißfläche: Wenn die Schweißfläche vor dem Schweißen nicht ordnungsgemäß gereinigt und vorbehandelt wird, z. B. durch Entfernen von Oxiden, Fett usw., beeinträchtigt dies die Qualität und Festigkeit der Schweißnaht und führt leicht zu Rissen. Die Lösung besteht darin, die Schweißoberfläche ausreichend zu reinigen und vorzubehandeln, um sicherzustellen, dass Verunreinigungen und Verunreinigungen im Schweißbereich effektiv behandelt werden.
4. Unsachgemäße Kontrolle der Schweißwärmezufuhr: Eine schlechte Kontrolle der Wärmezufuhr während des Schweißens, wie z. B. zu hohe Temperaturen beim Schweißen, falsche Abkühlgeschwindigkeit der Schweißschicht usw., führt zu Veränderungen in der Struktur des Schweißbereichs und damit zu Rissen . Die Lösung besteht darin, die Temperatur und Abkühlgeschwindigkeit während des Schweißens zu kontrollieren, um Überhitzung und schnelles Abkühlen zu vermeiden.
5. Unzureichender Spannungsabbau: Eine unzureichende Entspannungsbehandlung nach dem Schweißen führt zu einem unzureichenden Spannungsabbau im Schweißbereich, was leicht zu Rissen führen kann. Die Lösung besteht darin, nach dem Schweißen eine geeignete Entspannungsbehandlung durchzuführen, beispielsweise eine Wärmebehandlung oder eine Vibrationsbehandlung (Hauptgrund).
Was den Herstellungsprozess von Lithiumbatterien betrifft: Welche Prozesse verursachen mit größerer Wahrscheinlichkeit Risse?
Im Allgemeinen besteht die Gefahr, dass beim Dichtschweißen Risse auftreten, beispielsweise beim Dichtschweißen von zylindrischen Stahlschalen oder Aluminiumschalen, beim Dichtschweißen von quadratischen Aluminiumschalen usw. Darüber hinaus ist beim Modulverpackungsprozess auch das Schweißen des Stromkollektors anfällig zu Rissen.
Natürlich können wir diese Risse auch durch Fülldraht, Vorwärmen oder andere Methoden reduzieren oder beseitigen.
Zeitpunkt der Veröffentlichung: 01.09.2023